クルマの内装パネルを3Dプリンターで作れます。(不完全版)VWゴルフ7のアウターバッフル②
昨日の続き
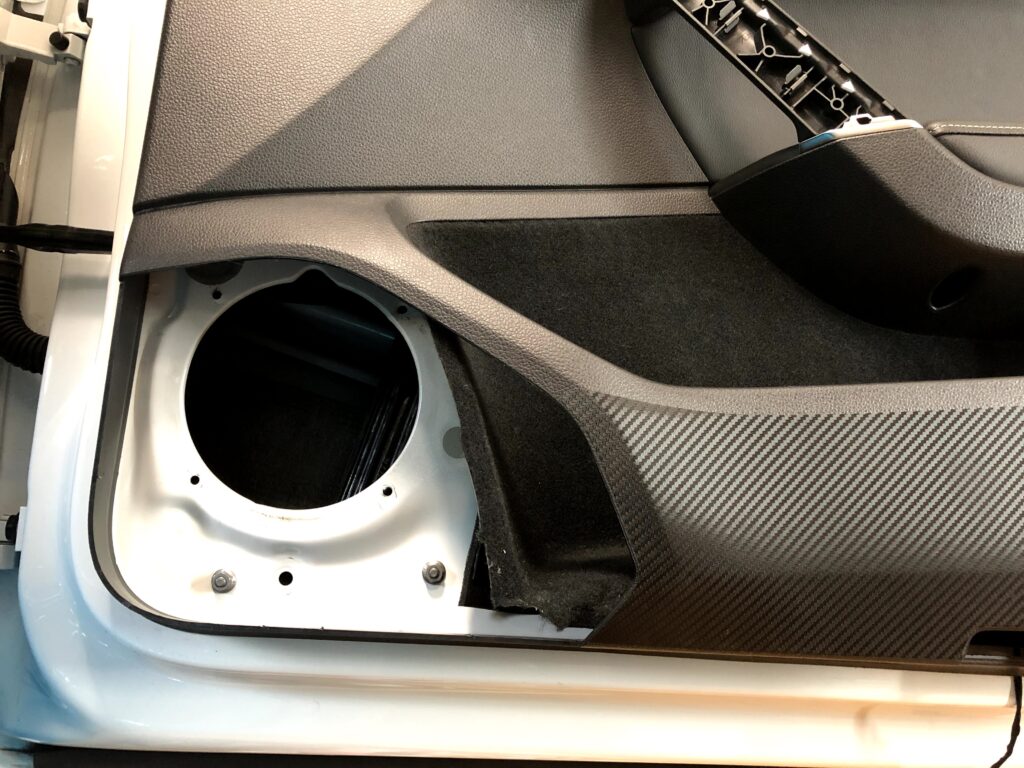
昨日はアウターバッフル部分を書きましたが、今日からはインナーバッフル部分
折角の3Dプリンターの造形なので、今回は実験で拡散を狙った特殊形状のバッフルを作ります。
スピーカー背面トンネルの壁面を凸凹にして排圧拡散を狙った形状にしたいのです。
最大の問題は、Fusion360でのモデリングw
それほど複雑ではない形状からやってみます。
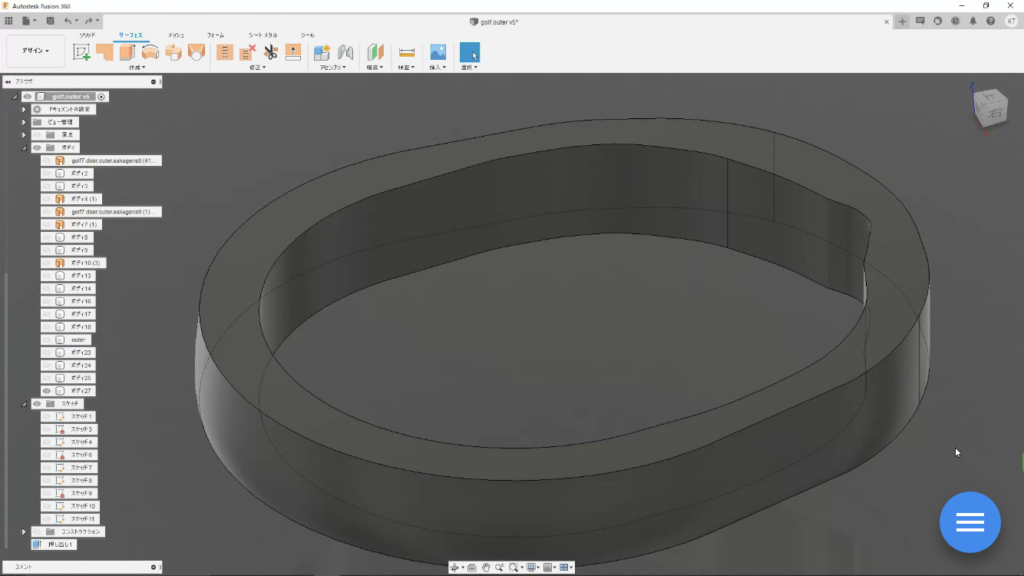
先ずは、ドアインナーパネルに接するベース部分は後でカットする前提で部厚めに
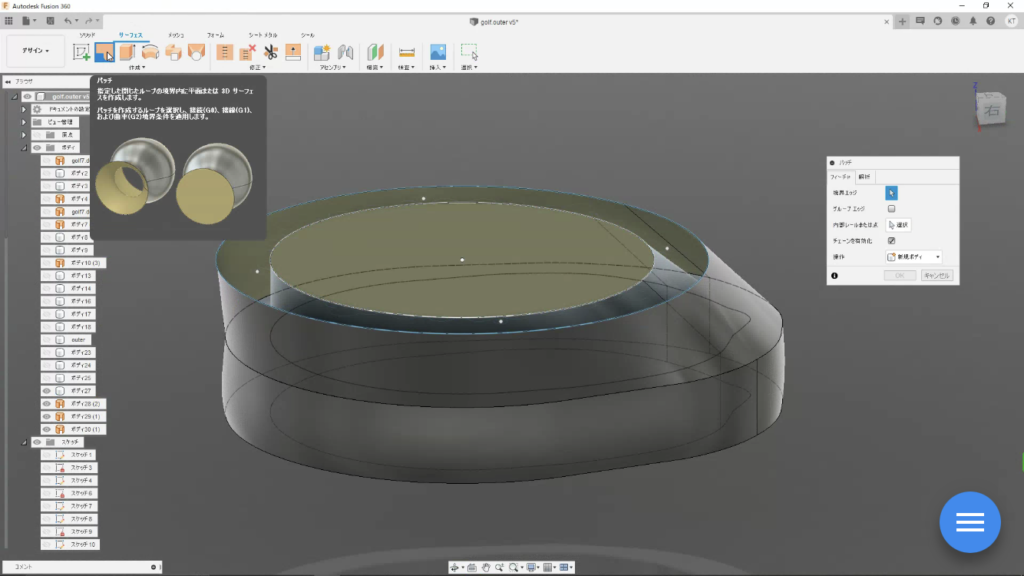
その上面とアウターバッフル底面のエッジをサーフェスモードの「ロフト」や「パッチ」で面を構成します。
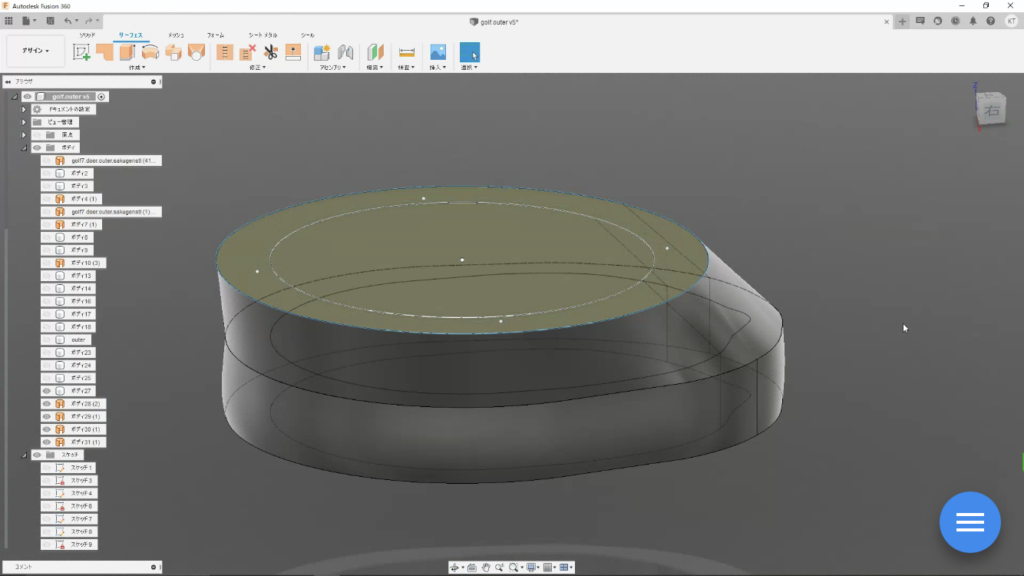
上面は真ん中も塞がっちゃうので
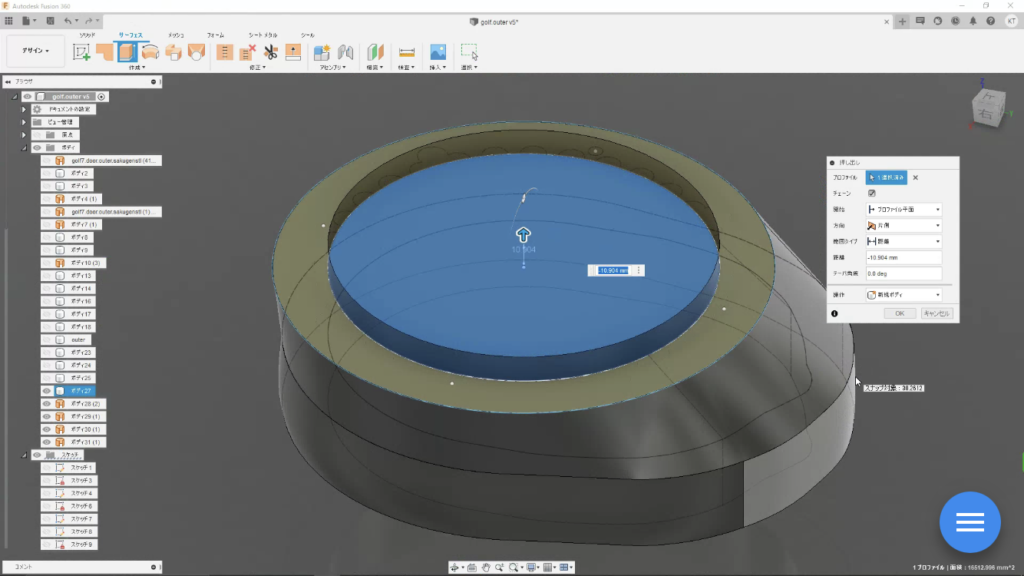
エッジを押し出して、
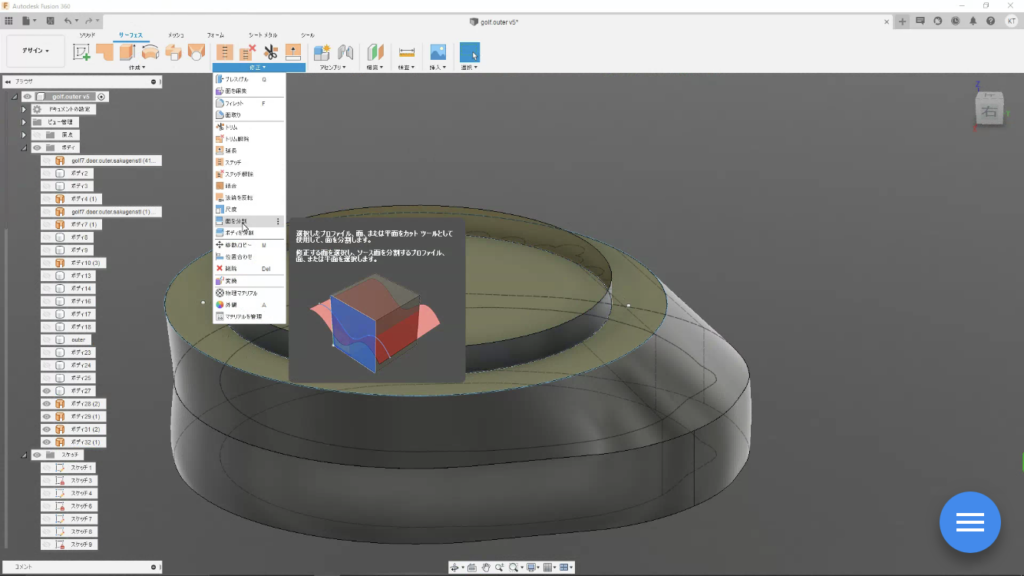
「面を分割」で真ん中部分を切り取ります。
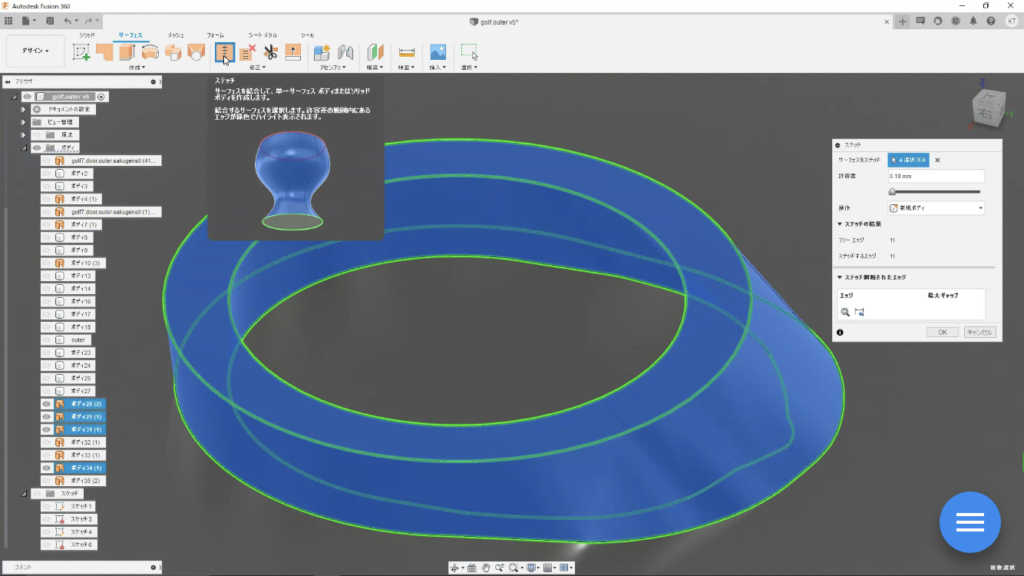
そのままだと、それぞれの面がバラバラなので「ステッチ」で縫い合わせる事で、中身の詰まったソリッドボディになります。
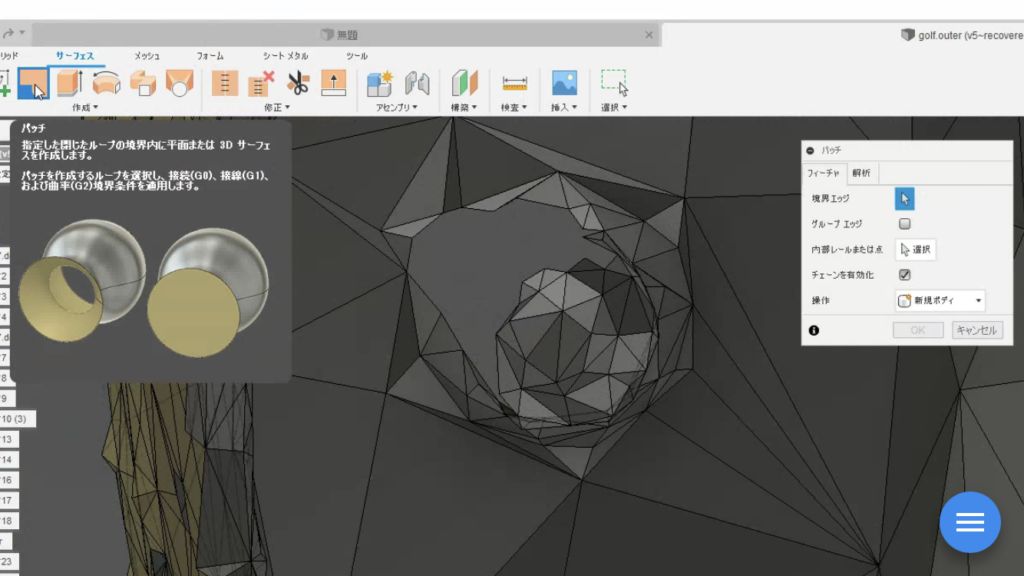
そのインナーバッフル底面をドアインナーパネルの凸凹面に沿ってカットする時に、カットしたい部分でドアインナーパネルデータに穴やはみ出しが有るとカット出来ずでエラーになります。
なので、重なる部分の穴を塞ぎます。
今回は「パッチ」で塞ぎます。
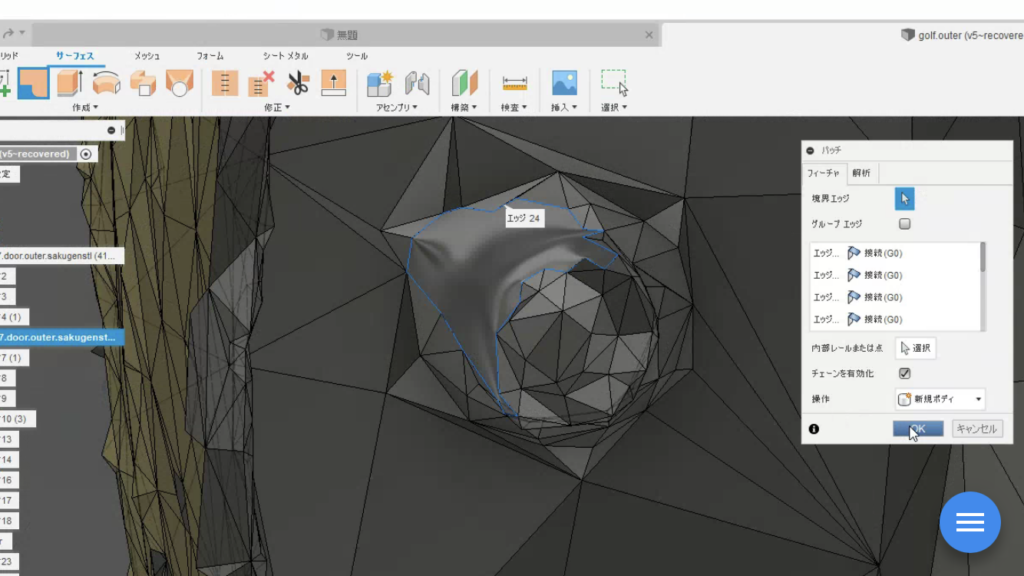
こんな感じでエッジをチェーン選択して自動で塞いでくれます。
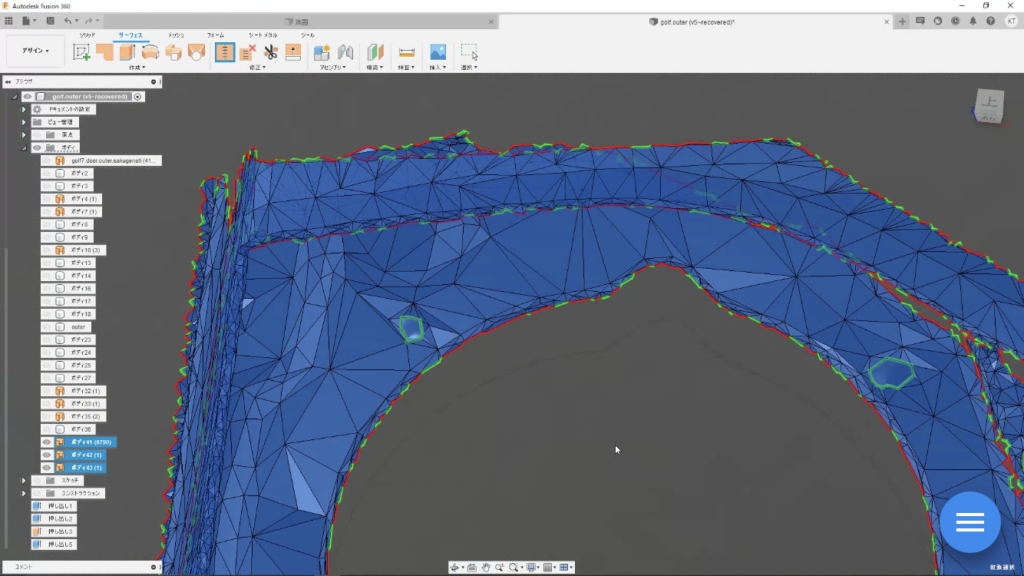
この塞いだ部分の面とドアインナーパネル面を「ステッチ」で結合させます。
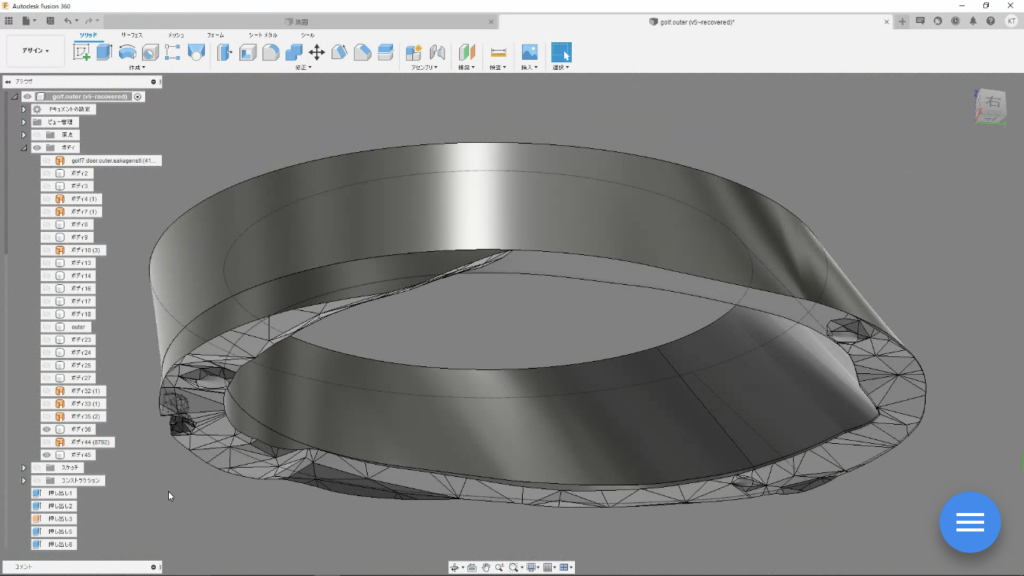
ソリッドモードの「分割」でドアインナーパネルの凸凹にフィットする形状にカット出来ます。
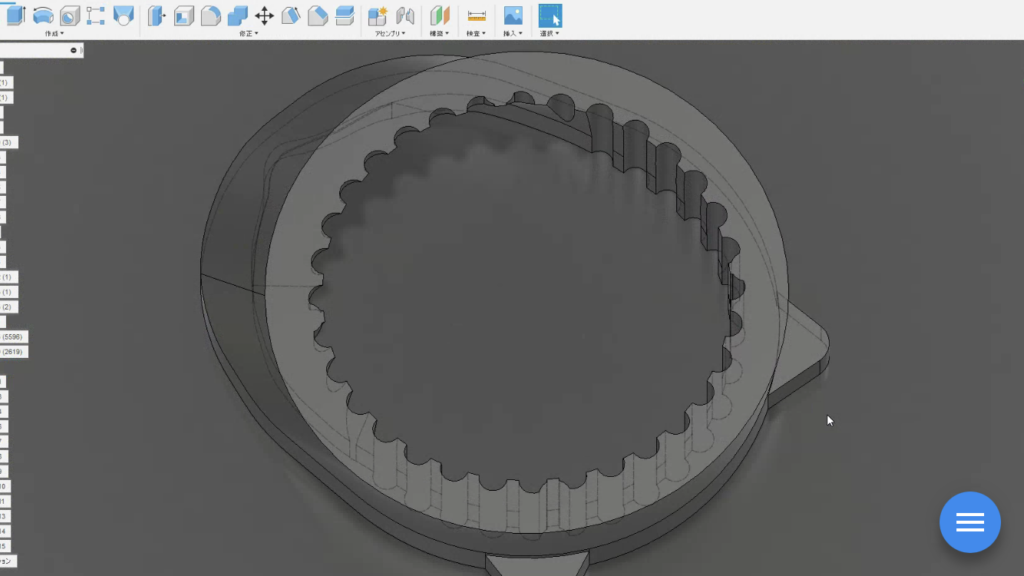
内壁は拡散効果を狙った特殊形状に
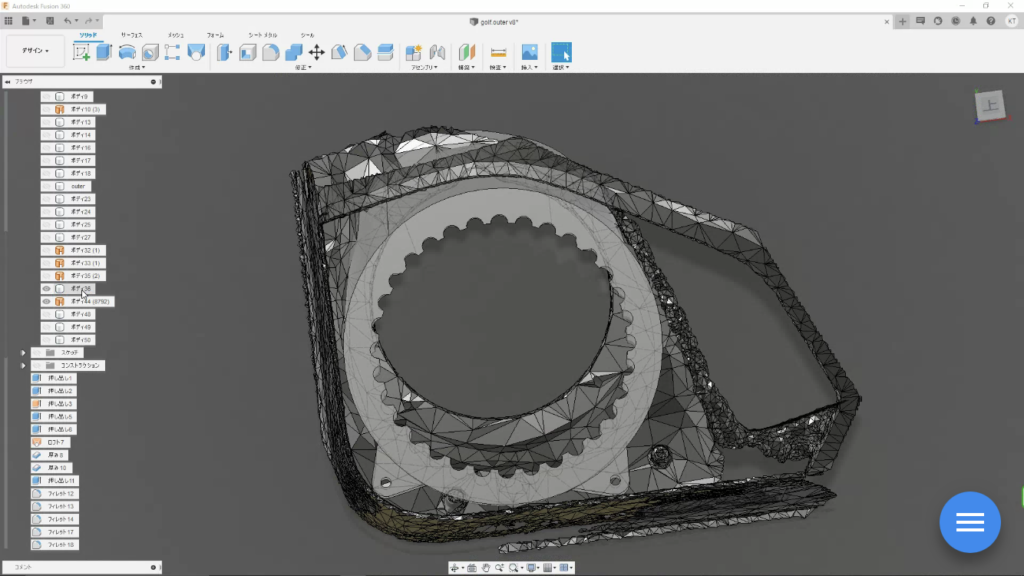
手加工でこんなバッフル作るのは大変ですが、モデリングさえ出来れば3Dプリンターが作ってくれます。
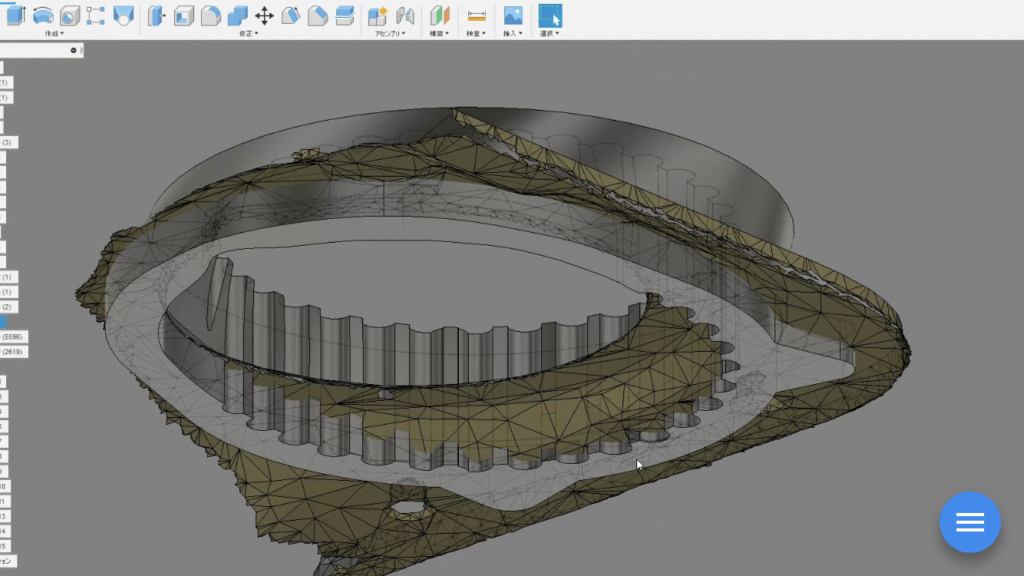
ちなみに、この形状のまま「ボディ分割」を試みましたが
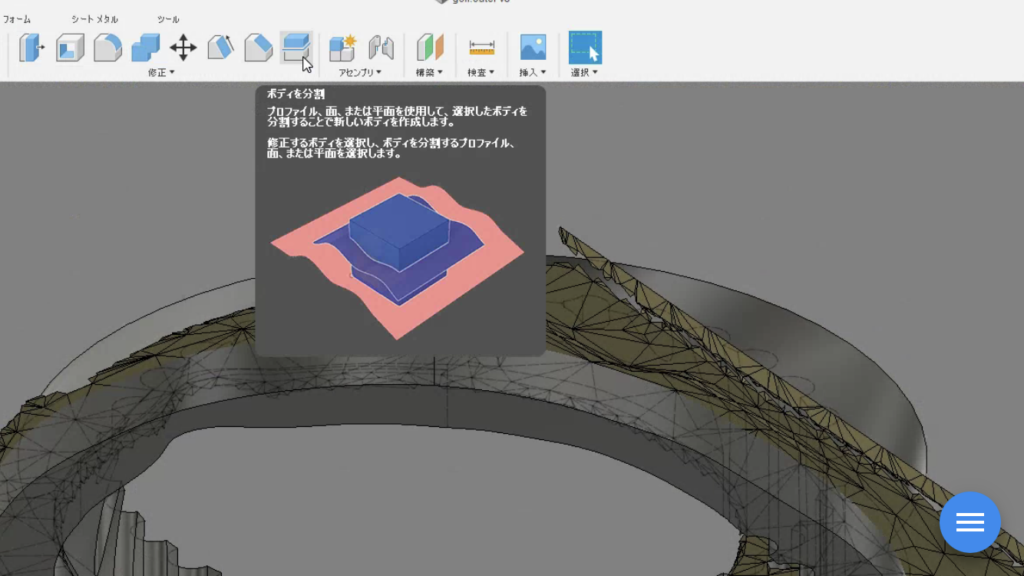
エラーに
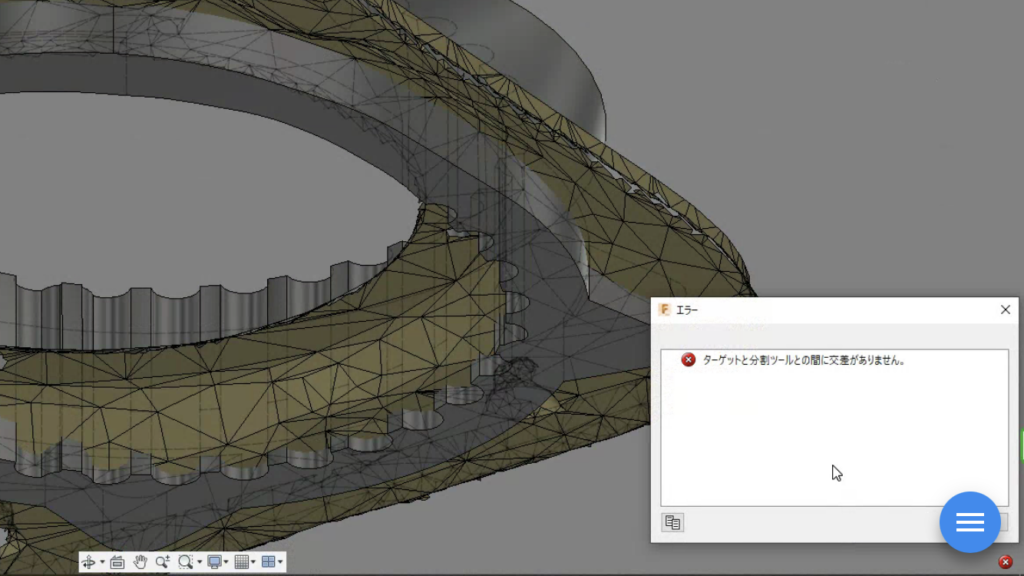
エラーの理由が交差が有りませんとなってますが、なんとなく計算がしんどいのかな??と思い
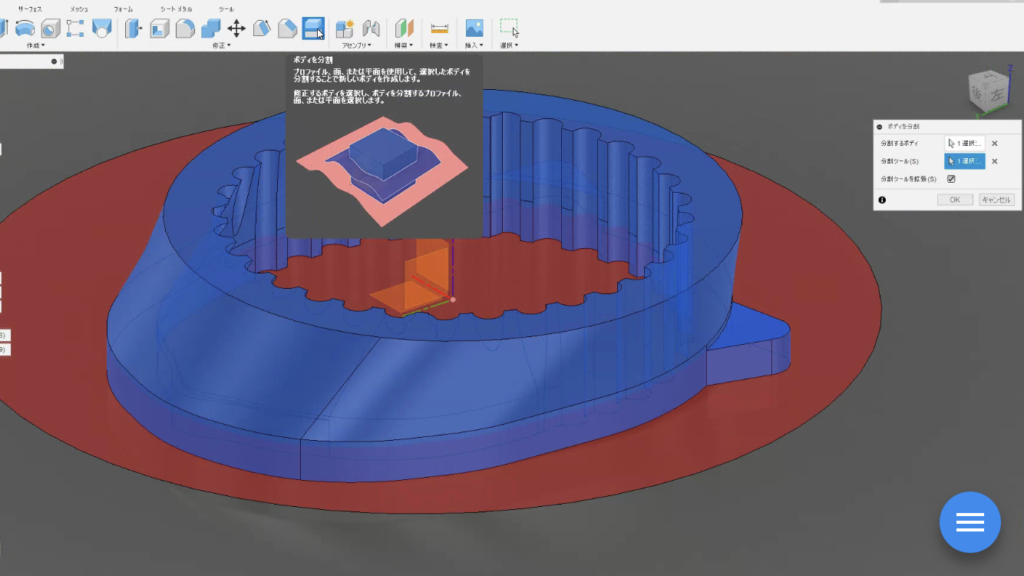
関係ない部分を出来るだけ分割して軽量化
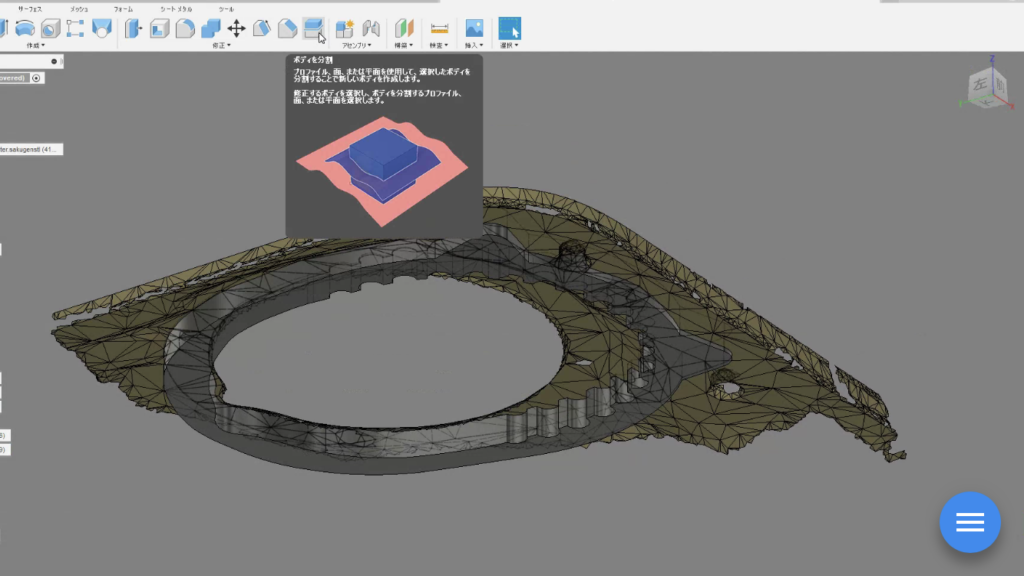
薄い状態で再度「ボディ分割」を試すと
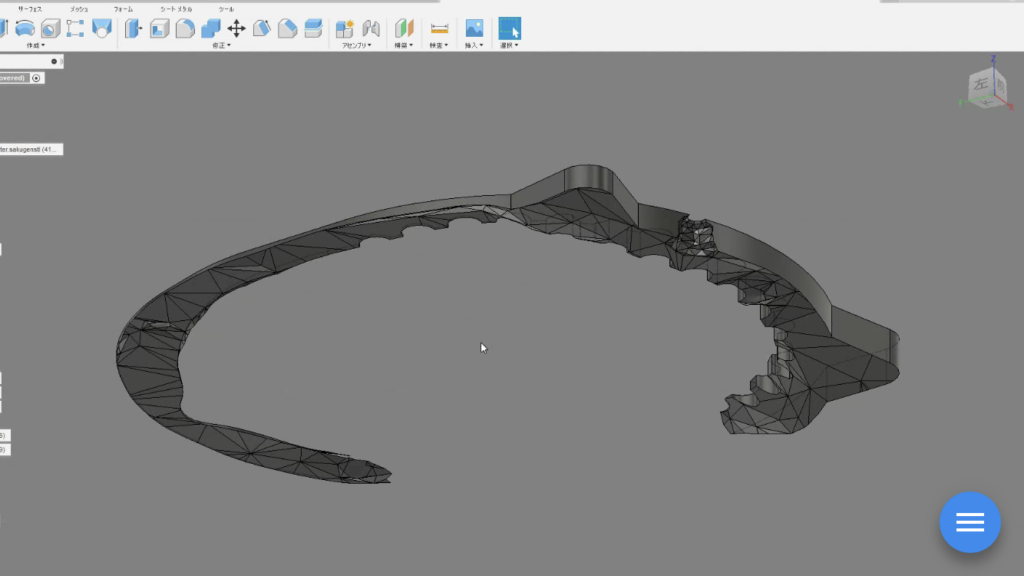
見事に成功
やはり出来るだけシンプルに余計な負担を掛けない事が成功への近道なのかな?
後は埋め込みナット部分とバッフル固定フランジ部分をモデリングして完成
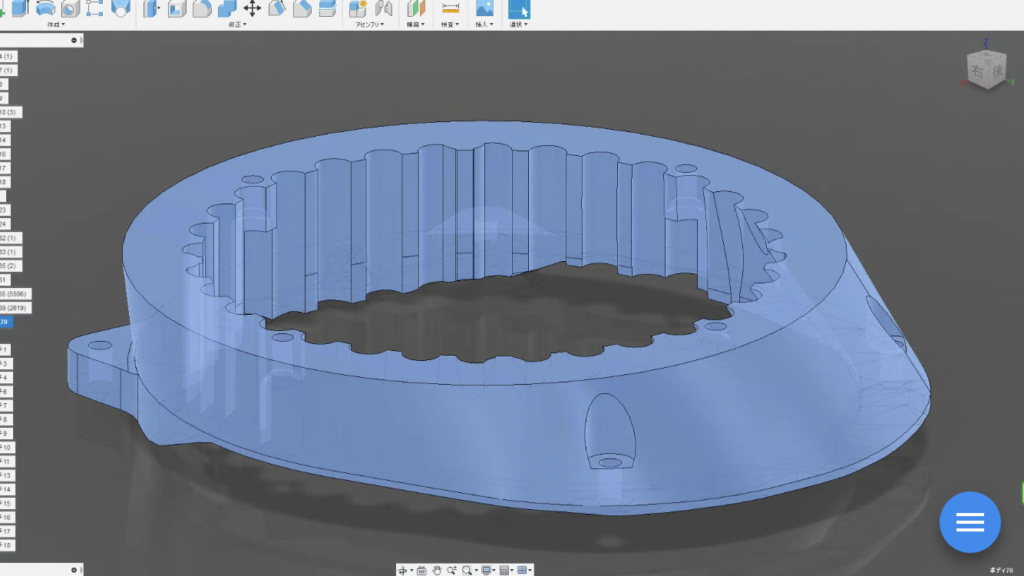
何度か木工では凸凹拡散バッフル試してるので間違いなく音響効果は良いのですが、作るのは大変w
Fusion360を駆使出来れば楽勝なんでしょうが、まだまだ修行が足りません。
次は完成編かな(^^)/